Piezoelectric Film Sensor (Picoleaf™)
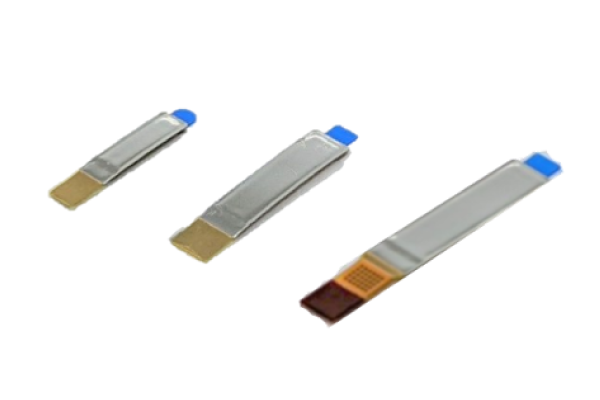
Technological advances have improved cleanliness and comfort in our daily life, and textiles are no exception. Having said that however, although conventional antimicrobial and deodorant treated fibers are both safe and functional, they had problems such as the environmental load of chemical agents used for efficiency and effectiveness in production process, functional degradation over time, and environmental pollution at the time of disposal. To solve these problems, PIECLEX Co., Ltd., a company that was jointly launched by Murata Manufacturing and Teijin Frontier, developed “PIECLEX,” an innovative fiber with a completely new concept of “Stretch-driven Antibacterial.”
PIECLEX holds its unique potentials different from conventional fabrics; however, due to its novelty of concept, there were plenty of issues of its own in the development and productization stages.
For this “Technology Explainer Section,” we invited Mr. Shiomi, who is responsible for the team carrying out the production and development, and Mr. Takumi, who is in charge of product development and evaluation to discuss the advantages of PIECLEX, the inspiration behind its development, and the untold development story of its productization.
--PIECLEX is a special product made from a fabric that generates electricity. Please tell us how Murata, an electronic component manufacturer, decided to develop textiles, and how Mr. Takumi and Mr. Shiomi became involved in its development.
One of the focuses of Murata was the piezoelectric effect of polylactic acid and the company successfully productized “Picoleaf™,” a kind of film sensor, which has piezoelectric properties. Subsequently, the company started the development of a filament sensor. At that time, there also was a boom in Wearables, so we approached many potential customers, with a lot of electrical characteristics data in hand. However, we could not close any deals. Then one day, one of our team members paid visit to a socks manufacturer. He was told, “Our biggest headache is bacteria.” That rang the bell. He thought “If we took away all the electrodes from the sensor, leaving just threads to make fabric, could bacteria be killed by the effect of electricity?” That was all about how PIECLEX development got started.
By the way, the voltage generated by PIECLEX ranges from several volts to roughly tens of volts, which is a level that humans do not perceive. Compared to static electricity, which is said to reach about 3,000 V, this is an extremely small amount of energy. However, its electricity is sufficient to inhibit microbial growth, in other words, the fabric exerts antimicrobial effect.
PIECLEX |
---|
Several volts to tens of volts |
Static electricity | |
---|---|
1,000 V | Don’t feel at all |
2,000 V | Feel slightly |
3,000 V | Feel a sting |
* Safety regarding cytotoxicity and sensitizing potential was verified at Japan Food Research Laboratories.
--There are many products that claim to be antimicrobial and deodorant. Please tell us about the advantages of PIECLEX over such rivals.
PIECLEX has two major advantages. The first is a semi-permanent antimicrobial effect. Some materials are known to generate a voltage in response to an applied stress. This is called the “piezoelectric effect.” PIECLEX is a fiber that realizes antibacterial and deodorant properties with the electric power generated by the piezoelectric effect when the fibre is stretched or contracted. Compared to antimicrobial treatments using chemical agents, which can degrade due to washing and aging, the piezoelectric effect is degradation-free against washing process overtime, so its antimicrobial and deodorant effect is semi-permanently maintained.
Another advantage of PIECLEX is its environmental friendliness . First, the chemical agents that are often used in conventional antimicrobial products are not used in our manufacturing process, so it has less negative impact on the environment. In addition, piezoelectric reminds people of ceramic material, but PIECLEX is made of “polylactic acid (PLA)”, which is a plant-derived biodegradable plastic. Therefore, PIECLEX , when buried in the soil, in turn is degraded (biodegraded) by bacteria and microorganisms. As to the biodegradability of PIECLEX, we obtained the data that verify about 70 to 80% of bio-degradability after 6 weeks of compositing experiment. Finally, because PIECLEX can be circulated back to nature quite quickly, so no need of incineration which is notorious about CO₂ emissions.
As you see, PIECLEX is a highly functional fabric material that has distinguished antimicrobial effect and deodorant properties. At the same time, it is environmentally friendly, because of its superior recyclability, and best of all, no emission of CO₂.
--May we ask you about the challenges? Say, priority differences came up from the background gap between electronics and textile industries. And another, “Stretch-driven antimicrobial” is a totally unique function. That should require a quite original evaluation method versus those from existing electronics development process.
Among all the various challenges, most of all was how-to-evaluate the “cloth” product made with the fiber. In contrast to the electronic components that Murata specializes in, feel and texture matter for fabrics, which in nature is individual-dependent and season-dependent. Numerical data was not enough for validation. Therefore, we were requested to prepare lots of material samples, which were used to obtain the correlation data between human aesthetic senses versus physical numeric. Also, another challenge was how to measure the electric discharge generated by stretch and contract. Conventional antimicrobial evaluations were generally performed under motionless condition at a premise, which was not suitable for a “Stretch-to-Antimicrobial” kind of materials. Such was a case, we had to do it on our own, but of course, such test equipment is not available in the market. Accordingly, we had to design and fabricate one from the scratch.
We were grateful for Murata’s expertise ever accumulated through years of efforts in creating products from various materials. With the great support from the internal team that handles many kinds of materials, we developed the test equipment based on a particular jig, and then successfully established the testing method. In due course, collaborative system was established where Murata evaluate the electrical characteristics and antibacterial functions, while Teijin Frontier take care of evaluation of coloring and touch feel of the cloth material. This is the birth story of PIECLEX.
In this issue, we introduced the technical aspects of PIECLEX. Hope you understand the productization was realized not only based on Murata’s accumulated technologies and expertise, but also on in-house support that was a great motive. In the coming up issue, we take a deeper look into other aspects of PIECLEX, such as the potentials and future prospect of finished products, as well as a diligent approach to environmental issues as an affiliate company of Murata Group.
* As of June 2023, sales of “PIECLEX” is limited to Japan.